SuS-F
Sustainable Steelmaking – follow up
Project description
Hydrogen plasma smelting reduction (HPSR): – High-quality steel – in one process step – CO2-neutral with the use of green hydrogen and green electricity – from a (semi-)continuous process
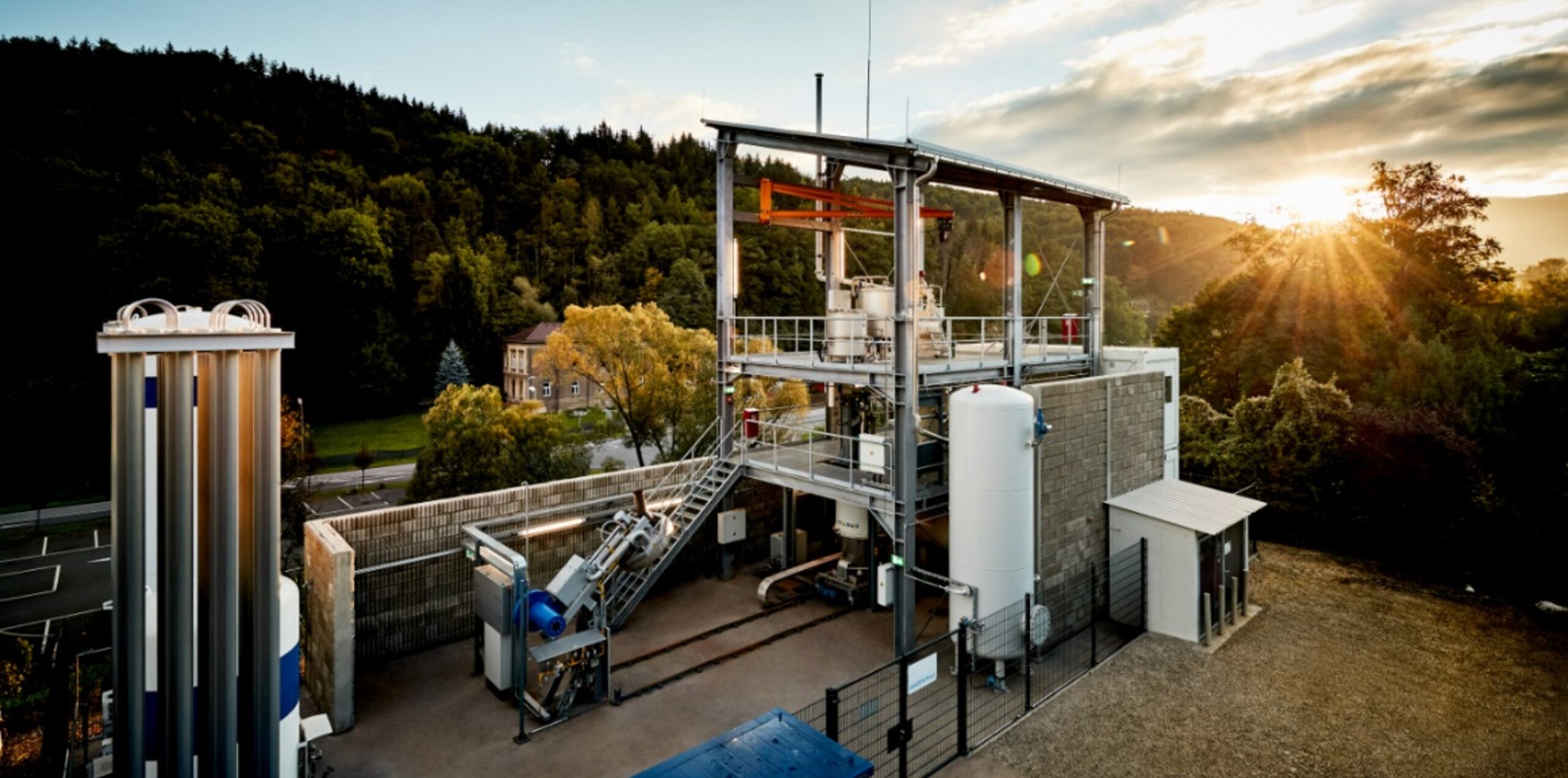
SuSteel Plant (© voestalpine Stahl Donawitz GmbH / K1-MET GmbH)
Factsheet
Contribution of partners
K1-MET GmbH
K1-MET GmbH is the Austrian COMET Competence Centre for Excellent Technologies in Advanced Metallurgical and Environmental Process Development and is driven by the Austrian steel industry. K1-MET is and was involved in various relevant national and international R&D projects regarding CO2 mitigation. The know-how being relevant for the current project SuS-F includes:
• K1-MET was strongly involved in the development of the existing HPSR demo plant in Donawitz.
• There is a lot of know-how concerning the use of hydrogen or mixtures between hydrogen and other inert gases as plasma gas for the reduction and smelting of iron oxides – both in laboratory and pilot-scale.
• Simulation know-how about the behaviour and the optimization of plasma arcs
• Broad technological know-how due to the strong network between scientific and industrial partners
Pirhofer Automation
Pirhofer Automation offers more than 15 years of experience in the area of process automation with PCS7, from version 6.0 up to the current version 9.1. The company’s area of activity encompasses the automation of industrial plants in the steel industry as well as pharmaceuticals production. For these tasks Pirhofer Automation predominantly uses Siemens automation systems with a focus on the field of process control technology. Particularly in this context, it is crucial to provide the best possible solution for the customer’s processes, based on the best available technology.
Montanuniversity Leoben
The HPSR process has been studied at the Montanuniversitaet Leoben since 1998. During this time, researchers have shown that the production of steel using a hydrogen plasma can not only reduce CO2 emissions significantly; it also has the potential to produce steel in a single-step process at lower costs than the standard integrated route. Up to now, six PhD theses and several master and bachelor theses have been carried out on this topic to further improve this potential key technology.
voestalpine Stahl Donawitz Gmb
As innovative leading company in the area of iron and steel making,, voestalpine Stahl Donawitz GmbH has a broad experience from many national and international R&D projects. The know-how relevant in context with this project includes: Expertise in element, mass and energy flow analysis of integrated iron and steel production, performance of material assessment and operational know how on gas cleaning and gas treatment. Further two pilot plants for the reduction of iron ores with hydrogen are located on site. The company assists K1-MET within the development of the HPSR process.
Voestalpine Stahl GmbH
As innovative leading company in the area of iron and steel making, voestalpine Stahl GmbH has a broad experience from many national and European R&D projects. The know-how relevant in context with this project includes:
– expertise in mass and energy flow analyses of integrated iron and steel production
– performance of laboratory reduction tests and material assessment
-and operational know how in iron and steel production, on gas cleaning and treatment and gas filling stations.
The company assists K1-MET within the development of the HPSR process.
Project video
Galery
© Voestalpine Stahl Donawitz GmbH / K1-MET GmbH
Publications
Hydrogen plasma smelting reduction process monitoring with optical emission spectroscopy – Establishing the basis for the method.
In the world of ever-increasing demand for carbon-free steel, hydrogen and recycling have an undeniable role in achieving net-zero carbon dioxide emissions for the steel industry. However, even though steel is one of the most recycled materials globally, the quantity of steel that can be made from recycled steel will probably not match the demand in the future. This in turn means that steel must also be produced from the conventional resource, the iron ore. Hydrogen has been proposed as an environmentally friendly alternative to carbon as a reducing agent. To tackle the problems related to the usage of hydrogen for this purpose, hydrogen plasma smelting reduction has been studied extensively in the last few years. This article aims to provide means for process control of the hydrogen plasma, which may show erratic and chaotic behavior during the smelting process. The method used is optical emission spectroscopy, with which the plasma can be characterized, its composition can be evaluated, and its temporal evolution can be assessed. This study sheds light on how the plasma behaves with different electrode gaps and flow gas compositions together with how the position of the arc with respect to the center of the crucible can be assessed. In Ar/H2 plasma, the plasma temperatures derived with OES varied between 4000 and 10000 K, and up to a 26% decrease in electron density was observed when increasing the electrode gap in 1 cm increments.
Source: Pauna H., Ernst D., Zarl M., Aula M., Schenk J., Huttula M., Fabritius T. (2022): Hydrogen plasma smelting reduction process monitoring with optical emission spectroscopy – Establishing the basis for the method. In: Journal of Cleaner Production 372 (2022) 13375.
Effects of the Electrodes’ Shape and Graphite Quality on the Arc Stability During Hydrogen Plasma Smelting Reduction of Iron Ores.
Reducing greenhouse gases (GHG), especially CO2, is necessary to counteract climate change. The European steel industry currently corresponds to 5.7% of the total EU emissions and must therefore minimize their GHG fractions in the future. One of the most promising technologies to eliminate CO2 emissions while directly reducing iron ore to steel in a single step is the hydrogen plasma smelting reduction. The stability of the plasma arc, which is determined by the properties and geometry of the graphite electrode, has a substantial impact on the process’ economic feasibility. To study the arc stability concerning the graphite quality, tip geometry, and electrode gap, a series of experiments is conducted. The results are evaluated to create stability maps and fields to identify stable process parameters. The geometry of the graphite cathode shows the primary influence on arc stability. Tips with a flat end (standard version) offering the most unstable and a machined step on the graphite cathode providing the most stable conditions. However, an additional coating to prevent side arcing leads to the deterioration of the arc. The two graphite grades tested, with different maximum grain sizes and price classes, show no great relevance to the stability of the arc.
Source: Ernst D., Zarl M. A., Farkas M. A., Schenk J. (2023): Effects of the Electrodes’ Shape and Graphite Quality on the Arc Stability During Hydrogen Plasma Smelting Reduction of Iron Ores. In: steel research int. 2023, 94, 2200818
Impact of Iron Ore Pre-Reduction Degree on the Hydrogen Plasma Smelting Reduction Process.
To counteract the rising greenhouse gas emissions, mainly CO2, the European steel industry needs to restructure the current process route for steel production. Globally, the blast furnace and the subsequent basic oxygen furnace are used in 73% of crude steel production, with a CO2 footprint of roughly 1.8 t CO2 per ton of produced steel. Hydrogen Plasma Smelting Reduction (HPSR) utilizes excited hydrogen states with the highest reduction potentials to combine the simultaneous reduction and smelting of iron ore fines. Due to the wide range of iron ore grades available worldwide, a series of hydrogen plasma experiments were conducted to determine how pre-reduced iron ore and iron-containing residues affect reduction behavior, hydrogen consumption, overall process time, and metal phase microstructure. It was discovered that, during the pre-melting phase under pure argon, wet ore increased electrode consumption and hematite achieved higher reduction levels, due to thermal decomposition. The reduction of magnetite ore yielded the highest reduction rate and subsequent hydrogen conversion rates. Both hematite and magnetite exhibited high utilization rates at first, but hematite underwent a kinetic change at a reduction degree of 80-85%, causing the reduction rate to decrease. In comparison to fluidized bed technology, it is possible to use magnetite directly, and the final phase of the reduction can move along more quickly due to higher temperatures, which reduces the overall process time and raises the average hydrogen utilization. A combination of both technologies can be considered advantageous for exhaust gas recycling.
Source: Ernst D., Manzoor U., Souza Filho I. R., Zarl M. A., Schenk J. (2023): Impact of Iron Ore Pre-Reduction Degree on the Hydrogen Plasma Smelting Reduction Process. In: Metals 2023, 13, 558.
In this work we investigate the feasibility and optimisation pathways for using oxide-filled consumable electrodes as both ore feeding system and reducing/melting arc carrier in the hydrogen plasma smelting reduction process. Similar in nature to Söderberg-type electrodes, but free of C-containing substances, this approach has the potential advantage of eliminating the carbon emissions stemming from conventional electric arc furnace electrodes while drastically simplifying the ore feeding into the process. Using a commercial welding setup with a 1.2 mm thick oxide-cored steel wire, area investigations indicate that approximately 50% of the introduced iron ore could be reduced to metallic iron at 100 A arc current under an Ar-10% H2 atmosphere independent from deposition time. The reduction efficiency was negatively affected by increasing arc current and it was increased by using the wire as the anode. Based on the performed variation of deposition parameters, microstructural characterisation results, high speed footage and first upscaling trials, the key scientific questions and engineering pathways for technological optmisiation towards future green steel production technology are outlined and discussed.
Source: H. Springer1, I. R. Souza Filho, L. Choisez M.A. Zarl, C. Quick, A. Horn, J. Schenk (2023): Iron ore wires as consumable electrodes for the hydrogen plasma smelting reduction in future green steel production. In: Sustainable Materials and Technologies, Volume 39, April 2024, e00785
Project News
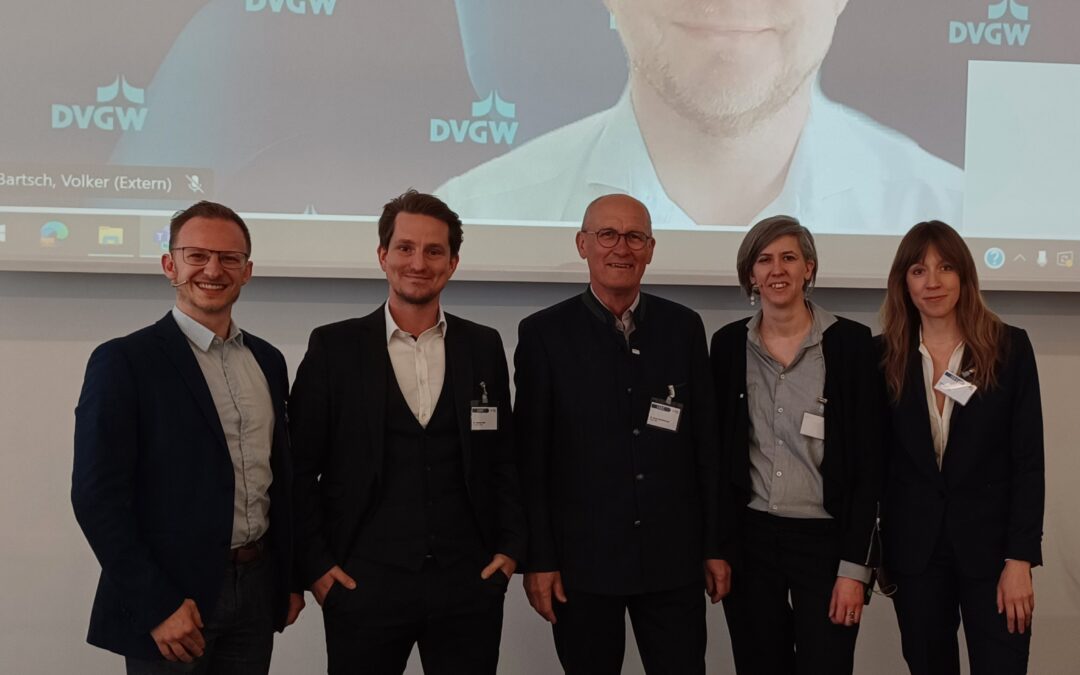
WIVA P&G Session @ ISEC 2024
Hydrogen – A key factor to a Sustainable Economic System WIVA P&G Session at the 3rd international Sustainable...
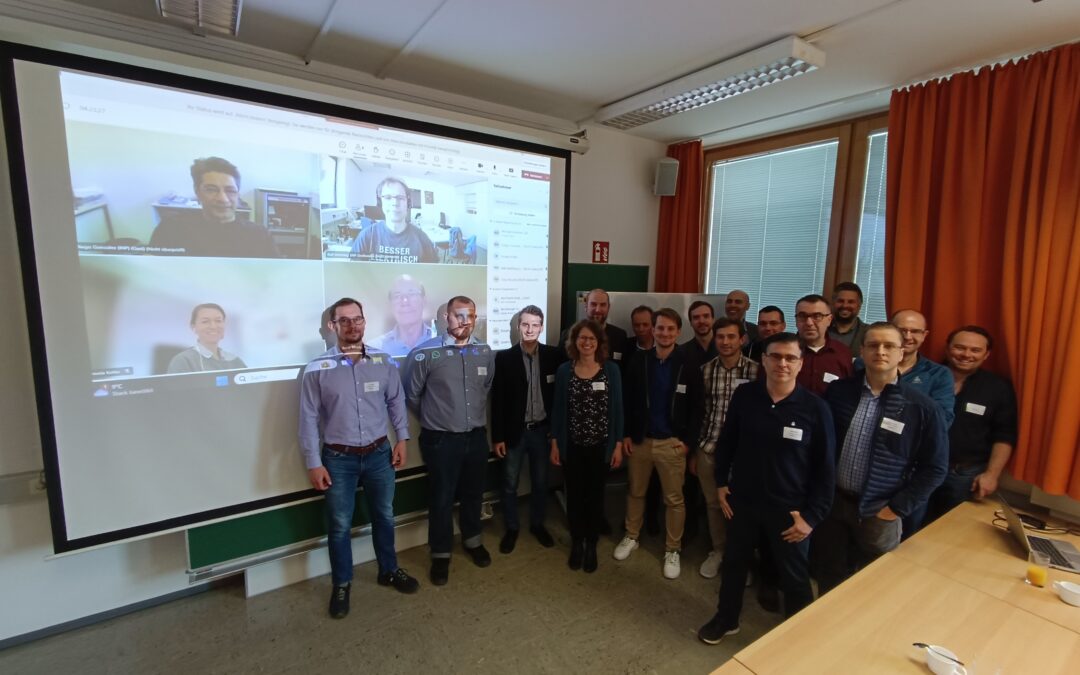
#GreenSteel #Research #Innovation
Exciting insights were shared at the hybrid Dissemination Workshop in Leoben, where 31 participants converged to...
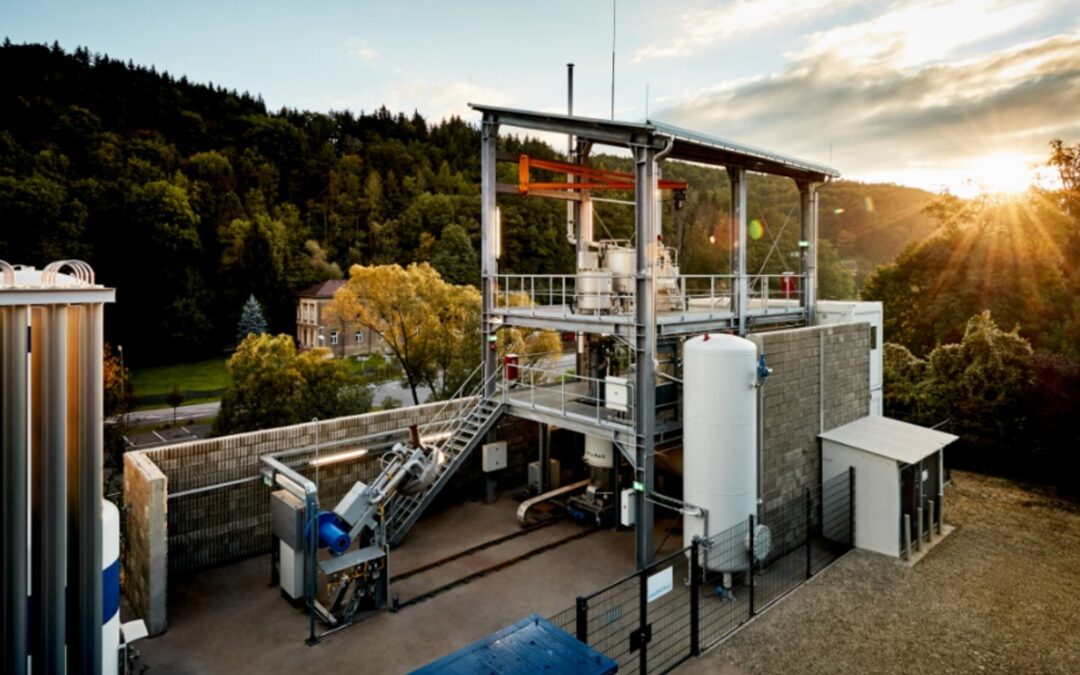
SuS-F: Iron ore wires as consumable electrodes for the hydrogen plasma smelting reduction in future green steel production
In this work we investigate the feasibility and optimisation pathways for using oxide-filled consumable electrodes as...

Hydrogen Plasma Smelting Reduction: The Way to Carbon Free Steelmaking
Die „Metallurgy & More“ Konferenz 2023 konzentrierte sich auf betriebliche Aspekte, neue Entwicklungen und...
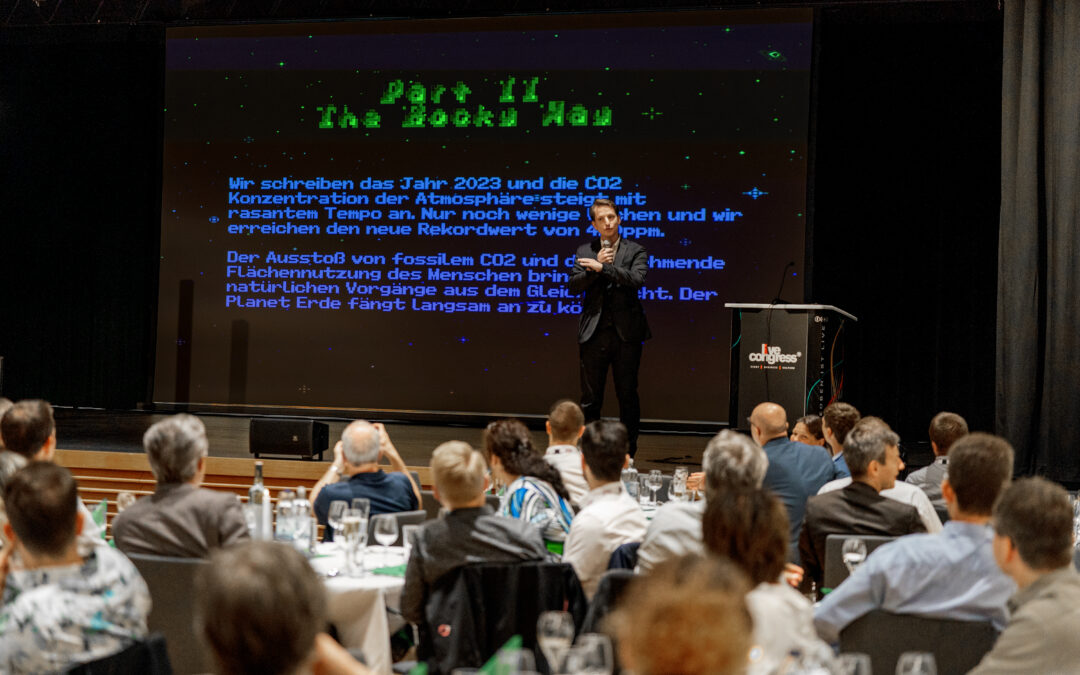
Die Revolution in der Stahlindustrie: Der (steinige) Weg zum grünen Stahl.
Im Rahmen der 57. Metallographie Tagung 2023 hielt Michael Zarl (Projektleiter SuS-F) einen Gastvortrag unter dem...
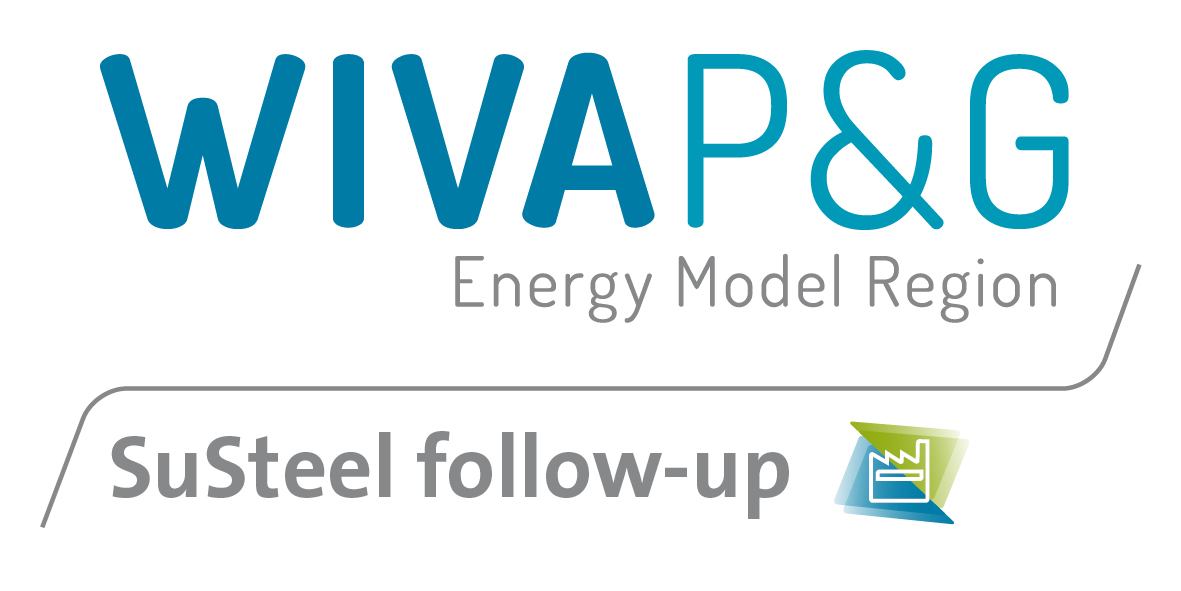